Simkomat
вендинг размером с принтер
Симкомат — особый проект для нашей команды. В течении нескольких лет мы вошли в состав распределенной команды и взаимно проявили свои способности доверять, держать обещания и достигать растущей планки качества.
Наш клиент
Компания, которая разрабатывает и реализует специализированные решения в сфере вендинга сим-карт с 2009 года. За 9 лет их команда прошла емкий стратегический путь и к 2018 году родилась уникальная, логичная, изящная концепция инфраструктуры по продаже сим-карт.
Идея
Симкоматы стоят повсеместно: аэропорты, вокзалы, супермаркеты. Пользователь приобретает подходящий тариф заранее в web, получает уникальный QR-код, показывает его любой стойке Симкомат и тут же получает сим-карту. Так же можно приобрести сим-карту непосредственно у Симкомата, подключившись к Wi-Fi который он раздает. При подключении к Wi-Fi на экране смартфона появляется окно captive portal и пользователь покупает симку, следуя набору подсказок.
MVP
В ходе интенсивных переговоров принято решение создать минимально жизнеспособный продукт (MVP). Он проверит ряд гипотез в ходе выставок и презентаций целевой аудитории. Необходимо убедиться, что после запуска дорогостоящей разработки, серийного производства и рекламы устройство будет востребовано на 100%. Если результаты не прогнозируют успеха, значит нужно углубляться в тему, не теряя сотни тысяч долларов.
Заказчик сам инициировал разработку дизайна и менеджмент у своего партнера. В этом процессе были выполнены такие задачи:
• Формулирование требований к устройству, функциям и прошивке.
• Разработать эргономическую компоновку устройства.
• Разработать визуальный образ, прорисовать экстерьер.
Поскольку на старте взаимодействий доверие друг другу было основано исключительно на рекомендациях, контролировать работу нашей команды предстояло команде из другого города. Они должны были проконтролировать: все что они заложили в эргономику и дизайн в картонных моделях, в точности реализуется нами на действующем прототипе.
Подбор электронных компонентов запустили параллельно с дизайном и эргономикой. В ходе плотной работы всех участников появился концепт — красивый и практичный. Минималистичный черный корпус с белым фасадом.
Мы оценили какой будет технология серийного изготовления: всем известная технология гибки металла, сварки и порошковой окраски. Такая технология не подходила для MVP: слишком много подготовительных работ и финансовых затрат на оснастку. Принято решение изготовить первый прототип по совершенно другой технологии. Внешний красивый корпус из панелей МДФ с 3D — фрезеровкой и стальными закладными. Внутренняя рама — стальная, сварная из нескольких деталей.
В прототипе были использованы стандартные электронные компоненты из магазинов. Они были громоздкими и не удобными к размещению. Не подходящие интерфейсы для подключения к системе приходилось компенсировать переходниками. Мы тратили драгоценную память микроконтроллера на лишние строки кода чтобы «подружить» все устройства.
Меньше чем за месяц была определена компоновка и выполнен дизайн симкомата. Параллельно этому процессу мы разрабатывали электронную плату управления. Далее механический дизайн. Дизайнерами предполагалось сделать лючок на боковой или задней панели для обслуживания. Инженерный коллектив увидел в этом две основных проблемы:
•Компоненты плотно распределены по всему объему. Размер лючка при размещении в любом месте корпуса не давал доступа ко всем компонентам.
•Лючок в красивом исполнении нуждался в технологически сложном проеме в корпусе и визуально был лишней деталью.
Мы искренне сопереживали всем будущим техникам, которым предстояло обслуживать симкоматы. Так родилась та самая концепция — фасад на выдвижной раме. Такое решение открывает доступ ко всем внутренностям с пяти сторон. Кроме того, упрощает отдельные детали, ускоряет сборку и положительно влияет на экстерьер.
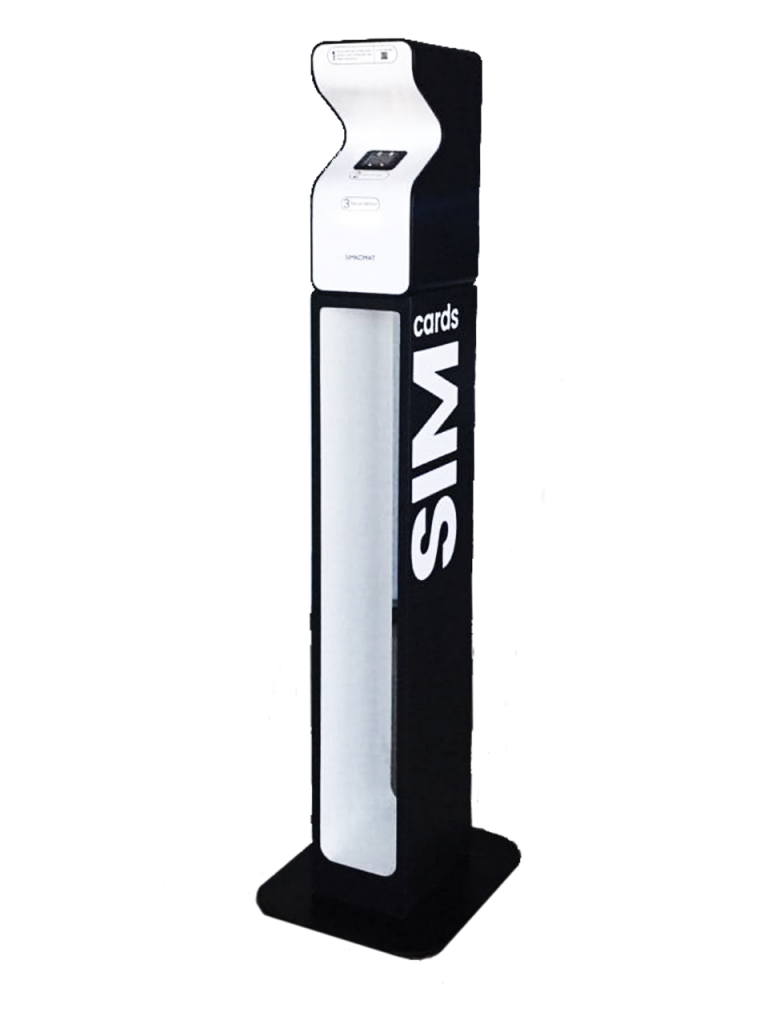
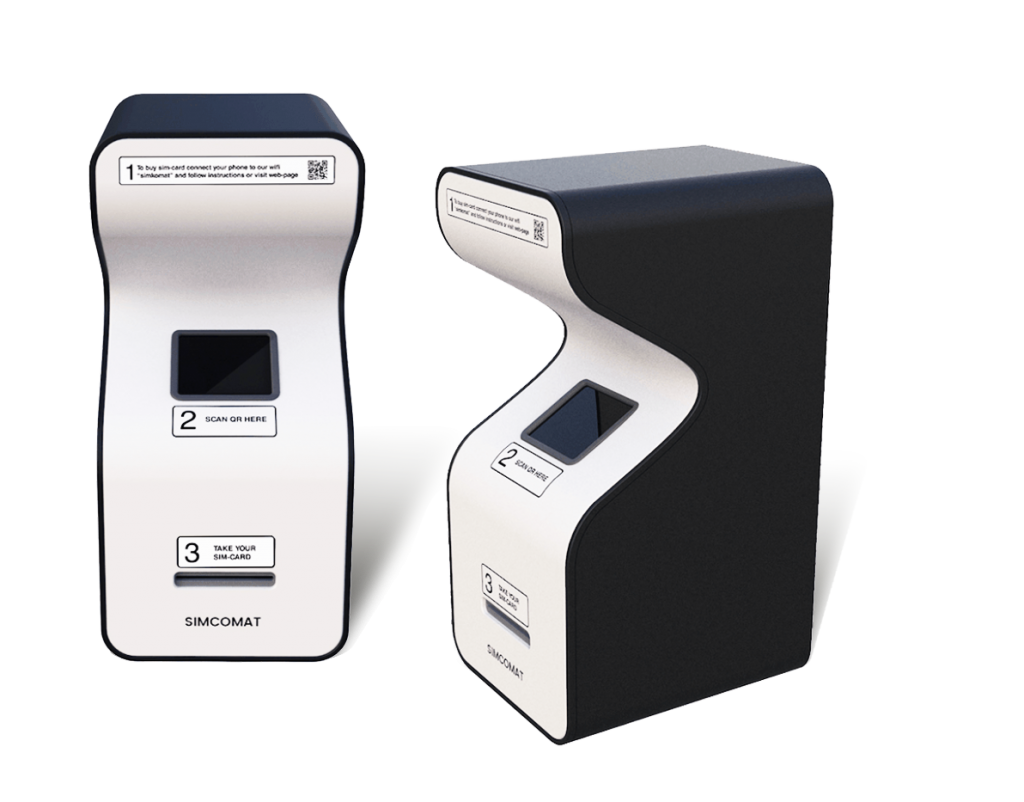
Сборка в CAD, разбивка основных элементов на технологичную сборную конструкцию, подготовка технической документации. Изготовление, сборка, окраска, запуск, отладка, тесты, доработки. Как итог — спустя три месяца со старта работ над MVP — приёмка и отправка на исследовательские мероприятия.
Серийная версия Simkomat
Спустя 10 дней после отправки MVP был подписан контракт на разработку серийной версии:
•Должен быть спроектирован так чтобы производиться в максимальном темпе. Все затраты на материалы и человеко-часы в производственном процессе оптимизированы.
•Работа в реальных условиях. Все вычислительные и мощностные характеристики электроники должны иметь запас. Все сценарии штатных и нештатных ситуаций должны быть многократно отработаны.
•Программное обеспечение оптимизировано на все сценарии работы.
•Разработан прозрачный сметный план производства, тестирования и упаковки. Все процессы описаны инструкциями.
•Нужно составить спецификации на компоненты и материалы, план производства. Коллаборация в общий CRM, потому что закупка компонентов и контроль за прогрессом осуществляется заказчиком.
В первую очередь мы сделали работу над ошибками в MVP, составили ряд требований к устройству после испытаний боем. Например, немного изменили форму корпуса чтобы считывание QR-кода не вызвало трудностей и добавили вентилятор со скрытыми воздуховодами.
Конструктив MVP не подходил для повсеместно доступной технологии лазерной резки и гибки металла. Поэтому симкомат проектировался заново.
Особое технологическое неудобство доставлял внешний корпус: нужно загнуть 4 красивых радиуса и попасть во все размеры. Оказалось, что у подрядчиков по гибке, не смотря на то, что их очень много, в принципе нет оснастки для радиусов. А с теми, у кого есть, не получилось договориться о сроках. Чтобы не добавлять лишних рисков проекту мы предложили клиенту вариант: наша мастерская спроектирует собственный станок, единственная задача которого — гнуть алюминиевые корпуса. Принцип гибки не сложный. Главное учесть все допуски, фактор перегиба и уделить внимание скорости процесса.
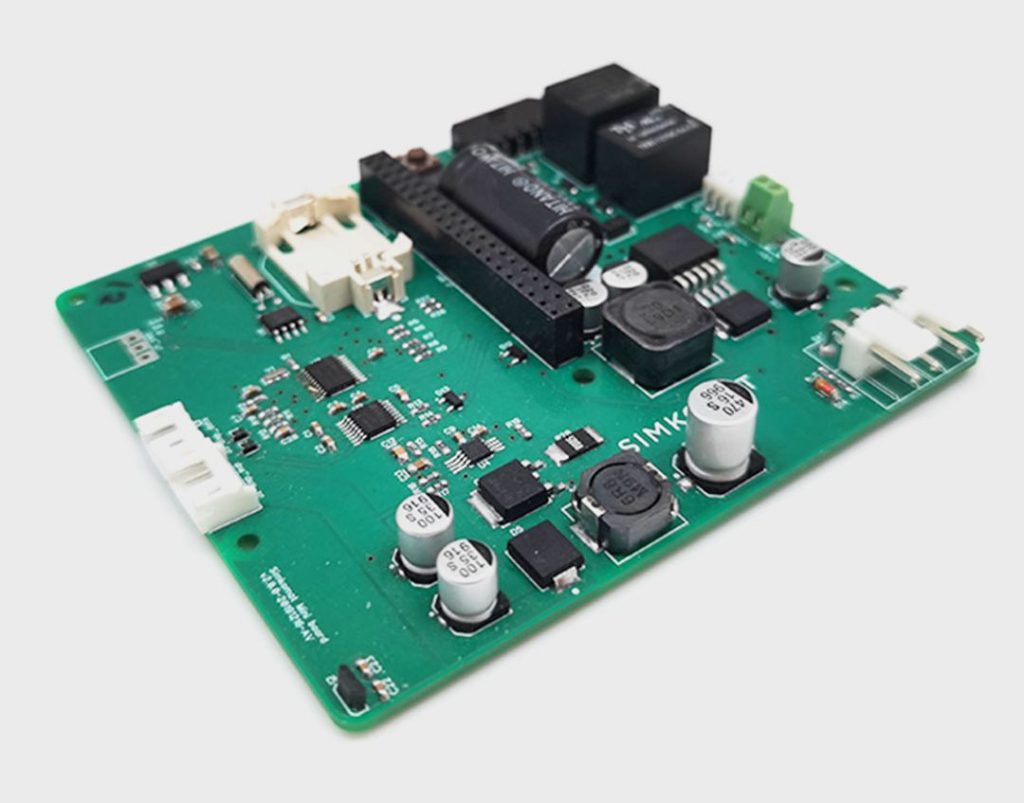
Для управления симкоматом мы разработали материнскую плату с микроконтроллером STM32, которая имела ряд интерфейсов и функций для управления всей электронно-механической периферией симкомата. В материнскую плату в специальный разъем вставляется микрокомпьютер Raspberry Pi, на котором развернута серверная часть с алгоритмами авторизации.
В частности, материнская плата управляет световой анимацией подсветки. В ней полный RGB спектр и поадресное управление пикселями — всего их 21. Это нужно для общения с клиентом интуитивно понятной анимацией. При открытии симкомата включается сервисный режим, в котором анимация отражает служебную информацию, что удобно при обслуживании симкомата оффлайн.
Многократное тестирование выявляло проблемные места в работе всей системы. Прежде чем появилась финальная версия материнской платы, было разработано и изготовлено 5 версий, которые отличались между собой набором функций, ключевыми компонентами и обвязкой.
Для производства передней панели симкомата из пластика разработан станок, который штампует нагретый до пластичного состояния пластик. Он выдерживает высокую точность и повторяемость. Это стало возможным благодаря десяткам экспериментов и углублению в физику сопротивления материалов, которые привели к тотальному контролю каждого параметра:
•температура в нескольких зонах;
•динамика нагрева;
•движение воздуха внутри;
•определенные; коэффициенты трения в разных местах между заготовкой и пуансонами;
•динамика охлаждения.
Даже динамика охлаждения, оказалось, влияет на деформации после извлечения. Несмотря на то, что отформованная заготовка остывает под прессом между пуансонами, если охлаждение было немного неравномерным — мы достаем кривой результат.
Конструкция внутренней рамы симкомата позволяет без труда заменить поврежденный фасад и отрегулировать плоскость в пяти местах с помощью пространственно распределенных креплений.
Итогом четырехмесячной разработки стали согласованные CAD-сборки, чертежи, схемы, спецификации компонентов, производственные сметы, списки подрядчиков. И одно устройство — согласованный серийный образец симкомата — golden sample.
Вскоре был заключен договор на изготовление сначала 20, а затем 80 штук.
Далее заказчик инициировал новую разработку. Нам предстояло разработать версию симкомата, которая будет встраиваться в корпуса третьей стороны — японской компании Rakuten. Технически это тот же симкомат, но с измененным внешним корпусом и несколькими узлами.
По техническому заданию доступ к симкомату в корпусе, в котором он будет стоять — сзади. Но симкомат невозможно обслуживать только с одной стороны из-за его плотной компоновки. Поэтому принято и согласовано решение разместить сзади ручку-замок. Это уникальное техническое решение решало 2 задачи:
• одностороннее автоматическое запирание при закрытии фасада, при этом происходит доброкачественное заклинивание рамы для исключения люфта.
• удобство открытия, которое происходит только с одной стороны — сзади.
Так как в России и Японии разное законодательство и стандарты безопасности, потребовалось немного изменить структуру устройства и материнской платы. Были так же предъявлены повышенные требования к надежности механической части. Мы активно работали над поиском решений и проходили множество кругов их согласования в сложной структуре огромной корпорации.
Мало произвести продукт. Мы постоянно балансируем между затратами на рекламацию с одной стороны и повышенную надежность, с другой. В нашем случае было оправдано снизить риски и сделать ставку на надежность: когда устройство преодолеет девять тысяч километров и встанет на свое рабочее место, оно выработает весь срок службы без ремонта. Ведь логистические и организационные затраты на рекламацию настолько высоки, что ломают бизнес-план.
Для минимизации рисков поломки разрабатываются тесты:
• защитного покрытия металла
• жгутов, отдельных устройств и электронных плат
• сотни циклов открытия-закрытия аппарата
• момента затяжки метизов
• работа после вибрационных испытаний
• работа при перепадах температур
• нагрузочный и ageing-тесты
Последнее — функциональное тестирование каждого аппарата перед упаковкой. В течении трех дней аппараты работают на стенде, происходит автоматическая выдача сим-карт, симулируется потеря GSM-сигнала и пропадает внешнее питание — все чтобы проверить что аппарат отработает все сценарии без сбоев.
Каждый аппарат имеет уникальный серийный номер и собственный аккаунт в CRM. Он содержит всю историю производства, эксплуатации и диагностических параметров, в том числе ageing-тесты. Если происходит замена, например, аккумулятора — появляется запись в аккаунте. Чек-лист проверки механических параметров имеет 7 пунктов и 69 подпунктов. Таким образом каждый аппарат имеет собственную историю от рождения до смерти. Мы даже запустили Telegram-бота, который по запросу присылал статус производства любому участнику кампании.
В результате, вписавшись в жесткие рамки сроков компании Rakuten мы выполнили и подписали golden sample of built-in Simkomat — встраиваемый вендинговый модуль.
Через неделю после этого заключили контракт на 180 устройств, выполнив его за три календарных месяца.
hello@rcprk.com